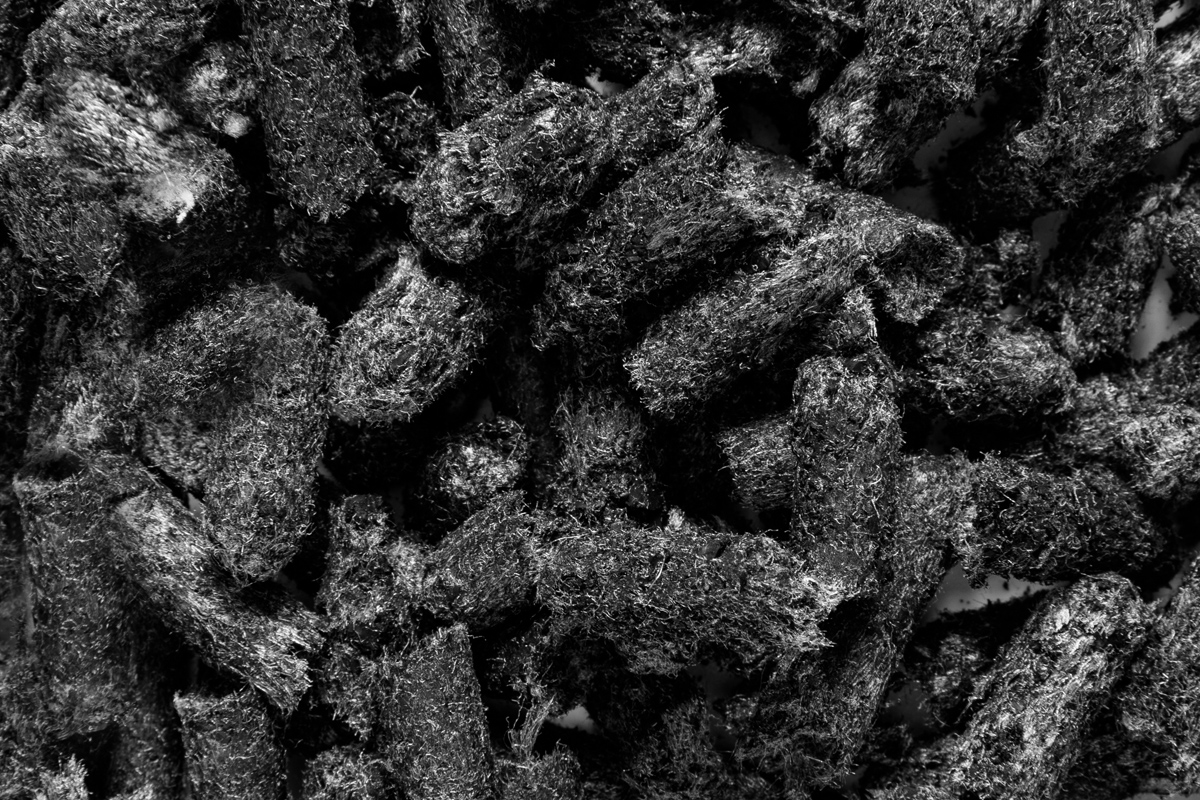
The article discusses some prospects for the development of the direction of use of high-strength textile cords used in the production of modern tires, which are massively recovered in the process of mechanical recycling of end-of-life tires to increase the reliability and durability of asphalt mixtures for the pavement of modern roads. As an example, some performance indicators were given for the use of the stabilizing and reinforcing additive SMAPOL® for mineral-asphalt mixtures, serially produced by RECYKL O.O. S.A. in accordance with the requirements of SYSTEM 2+ of evaluation and verification of constancy of performance of construction products, which is increasingly used both in Poland and abroad. In the production process of SMAPOL®, the multifiber blend, consisting of polyester, polyamide, aramid and viscose fibers, is optimized for the content of each type of fiber, activated and modified. This results in a product with exceptional functionality and efficiency.
The structure of mineral-asphalt mixtures (MMA) is in some cases considered a three-component system consisting of interconnected micro-, meso- and macro-structures. Microstructure is the structure of the asphalt binder (filler + asphalt), meso-structure is the structure of the asphalt solution (fine aggregate + asphalt binder), and macrostructure is the structure of the mineral-asphalt mixture (coarse aggregate + asphalt solution).
SMAPOL® is an ideal choice
The development of damage in asphalt layers of road pavements proceeds in three stages, described below, and leads to deterioration of their strength and deformation properties:
We are considering further Smapol production lines at our other plants. The first one could be built in 2025, and another one in 2026, with comparable production capacity.
Maciej Jasiewicz, Chairman of the Management Board of Grupa Recykl S.A.
At the same time, the higher the level of micro-defects accumulation, the higher the probability of macro-defects in the asphalt pavement structure due to transport loads and climatic factors.
Therefore, the improvement of the properties of the binder and asphalt solution, along with the strengthening of interfacial interactions at the boundary between mineral particles and asphalt, leads to an improvement in the physical and mechanical properties of asphalt mixtures, and thus the durability of road pavements.
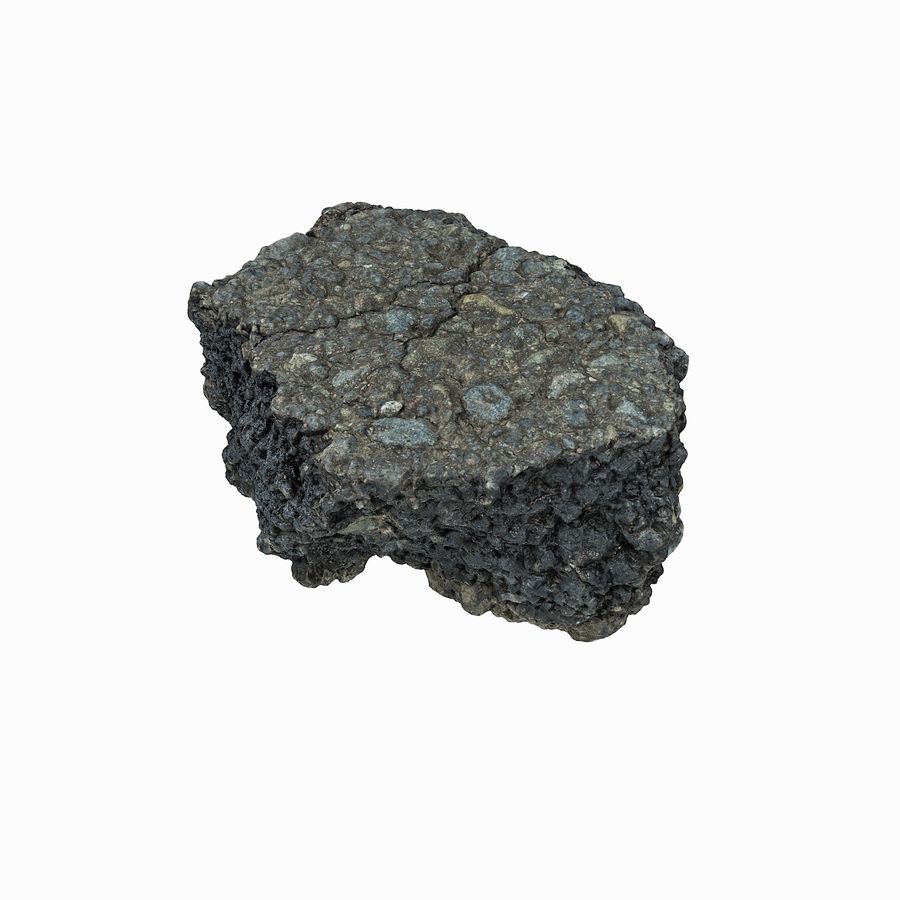
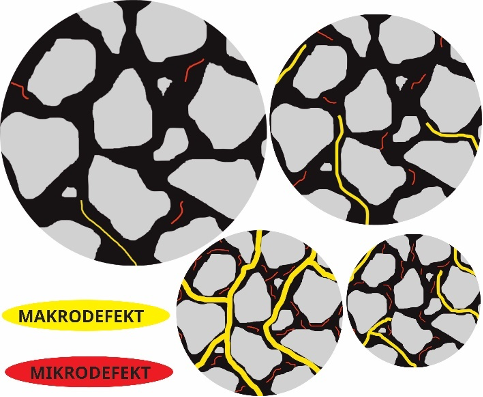
Therefore, improving the properties of the binder and asphalt solution, along with strengthening the interfacial interactions at the interface between mineral particles and asphalt, leads to improved physical and mechanical properties of asphalt mixtures, and thus the durability of road pavements.
Ways to improve endurance
The main way to improve the strength and durability of MMA is to modify the asphalt with polymeric components. All asphalts modified in this way can be divided into 2 large groups depending on the method of modification:
- Modified bitumens;
- Highly modified bitumens
The long-standing practice of using modified asphalts testifies to their effectiveness in increasing the durability of road pavements, but due to the constant increase in the load on modern roads, an increasingly higher degree of modification of asphalts is required, the consumption of polymers increases (for example, in the case of highly modified asphalts, the content of SBS-type polymer is more than 7%), which significantly increases the cost of road construction. For example, the cost of modified asphalt is 25-30% higher than the cost of ordinary road asphalt, and the cost of highly modified asphalt is already 40-50% higher. Given that the cost of asphalt is the main component of the cost of asphalt mixtures, this situation sometimes negatively affects the technical and economic efficiency of the entire road construction project (deterioration of the parameter “cost of pavement construction vs pavement durability”) and inhibits the widespread use of, for example, highly modified asphalts.
In addition, it should be noted that at a thermoelastic polymer content in asphalt of more than 6.5-7%, phase inversion occurs in the polymer-asphalt mixture, which negatively affects the workability of modified MMAs, requires an increase in the temperature of their production, placement and compaction, which reduces the environmental and cost efficiency of the process. It can be said that the effectiveness of modified asphalts has been exhausted in terms of increasing the degree of modification, and further improvement in the durability of road pavements requires innovative solutions in terms of developing methods for modifying the binder in MMA and improving their structural properties.
Modification methods
One such method is the technology of modifying MMA and asphalts with rubber from end-of-life tire processing, for example:
However, each method of such modification has its own advantages and disadvantages. For example, with the dry rubber modification method, the optimum asphalt content increases, and due to the deterioration of the interfacial interaction between rubber and asphalt, the rates of improvement in properties are small, and sometimes they worsen, which limits the use of this modification method to strictly defined climatic conditions of road surfaces. The method can be more effectively applied, for example, in hot, dry climates.
The widespread use of the wet terminal method of modifying asphalt with rubber is limited by the poor ability of asphalt modified in this way to be stored for long periods without delamination. At the same time, due to the low rubber content that results from the technological features of the production process of modified asphalt, the quality and properties of rubber should be constant and high, which calls into question the viability of this method of modification and the availability of raw material in the form of a selected group of tires.
The wet field method solves the above problems of modifying MMA with rubber from end-of-life tire processing, since it involves using the asphalt-rubber mixture immediately after its preparation, and due to the possibility of using a larger amount of rubber, problems with its quality and properties are not so noticeable. At the same time, given that the rubber does not dissolve completely, the resulting asphalt-rubber binder is not homogeneous, but consists of separate rubber particles swollen in oil fractions, which interact with each other and the mineral particles of the binder through partially modified asphalt films.
Thus, the prospects for further improvements in the strength and deformation properties of MMA, as well as in the indicators of their technical-economic and environmental performance, may be related to the development of the direction of optimization of the indicators of the formation of the asphalt solution structure at the micro- and meso-level.
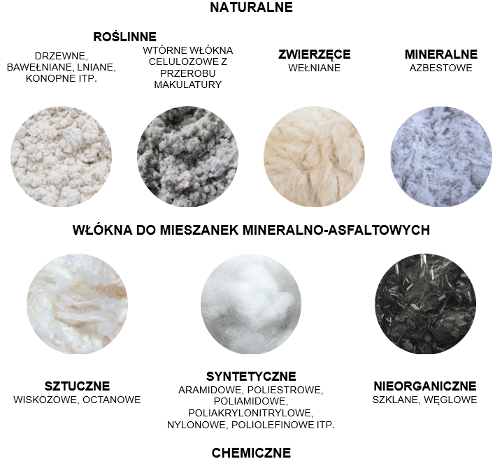
Another way to increase the structural strength of MMA is to reinforce it, for example, with various types of fibers, both at the micro- and macro-level.
In world practice, the following reinforcing fibers for MMA are most commonly used: mineral, such as basalt; synthetic, including aramid, polyester, polyamide, polyacrylonitrile, nylon, etc.; polyolefin, including polypropylene; glass; carbon.
There have also been a number of studies on the effect of a mixture of fibers (e.g., glass and polymer, mineral and synthetic, aramid and polymer/synthetic, such as Forta-FI® additive, carbon and polymer, etc.) on the strength properties of MMA.
In world practice, natural plant fibers (mainly cellulosic) are also widely used to ensure the stability of the asphalt binder (to prevent its runoff from mineral particles) in mineral-asphalt mixtures of discontinuous grain size during their transport, placement and compaction. However, due to the high absorption capacity of asphalt by cellulose fibers, they cannot significantly affect the strength and deformability properties of MMA at optimal asphalt content [1, 2].
In recent years, there has been increasing research into the effectiveness of using for microstructural reinforcement purposes at the micro- and mesostructural level of MMA synthetic fibers obtained by mechanical recycling of textile cords from end-of-life tires (polyester, polyamide, aramid and viscose) [3-6]. The high environmental and economic efficiency of their use is reported [7, 8]. However, this type of fiber has not yet gained widespread industrial use as an additive to asphalt mixtures due to the complexity of cleaning the fibers, as well as the complexity of obtaining an additive from them in a form suitable for efficient dosing and homogenization in the production of asphalt mixtures at asphalt plants.
The issue of mass production of the aforementioned additives has been solved by RECYKL O.O. S.A., which produces the stabilizing and strengthening additive SMAPOL® from this type of synthetic fiber.
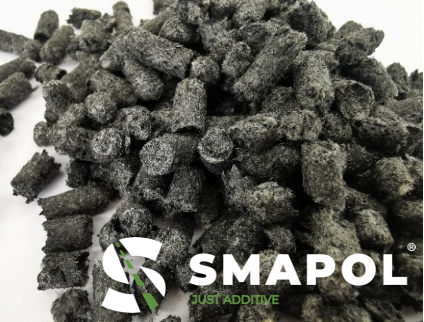
This type of synthetic fiber has optimal absorption properties and a low degree of swelling, which allows it to be used in MMAs of any structure and properties, including for microstructural reinforcement at the level of their micro- and mesostructures to increase strength and deformability. At the same time, the joint use of SMAPOL® with modified (highly modified) asphalts and rubber-modified asphalts to improve the long-term strength of MMA provides a significant synergistic effect.
MAIN ADVANTAGES OF USING SMAPOL® ADDITIVE
- Optimal technological properties: Prevents binder runoff in SMA and other discontinuous-grained MMA asphalt mixtures.
- Enhanced structural resistance: Increases rutting resistance, water resistance and frost resistance, and reduces the likelihood of low-temperature and fatigue cracking of MMA of all types
- Easy Dispensing: Can be dispensed with current dispensing equipment of any SMA stabilizer
- Easy storage: The increased hydrophobicity of the granule surface ensures that the granules retain their properties even after moisture penetrates the package, allowing storage without roofing
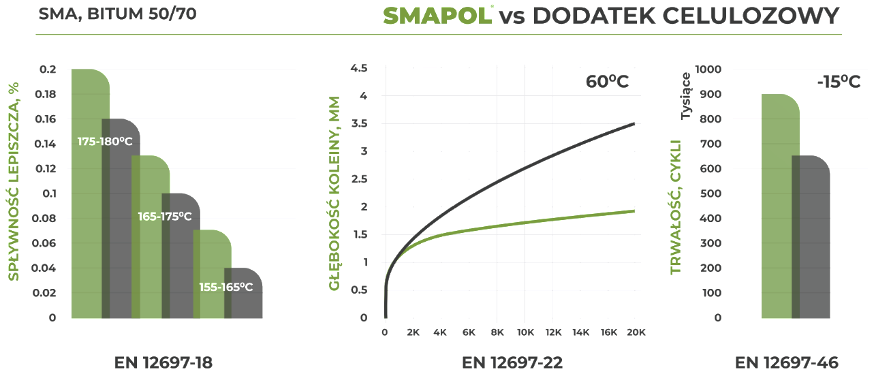
In contrast to the cellulose fiber-based additive, the SMAPOL® synthetic fiber-based additive, when increasing its content to 30% in the composition of the SMA mixture relative to the level of the cellulose additive content, provides an increase in its structural strength (up to 20-25%) and rutting resistance (up to 35-40%) with a simultaneous increase (up to 5%) in the water resistance index and resistance to thermal cracking (up to 10%). As the use of SMAPOL® synthetic fibers increases under conditions of optimal binder matrix saturation (for example, for SMA mixtures – up to 0.9-1.2%, for AC mixtures – up to 0.2-0.5%), the strength and deformability indices of asphalt mixtures will also increase.
Thus, by using SMAPOL® instead of cellulosic additives, we can count not only on a reduction in direct costs (the cost of SMAPOL® on the Polish market is lower than that of cellulosic additives by 1.6-1.75 times), but also on achieving a measurable annual economic effect by extending the life of road pavements by about 25-40%.
Therefore, the SMAPOL® story is just beginning!
References
- McDaniel R.S.: Fibrous additives in asphalt mixtures. NCHRP Synthesis of Highway Practice. Transportation Research Board, 2015, №. Project 20-05 (Topic 45-15), №475, 67 p.
- Sybilski D., Horodecka R., Bańkowski W., et al: Evaluation of the effectiveness of fiber addition to mineral-asphalt mixtures. GDDKiA topic TN-251. IBDiM, Warsaw, 2010, 89 p.
- Putnam B.J., Amirkhanian S.N.: Utilization of Waste Fibers in Stone Matrix Asphalt Mixtures. Resources, Conservation and Recycling, 2004, Vol. 42, 265-274.
- Sybilski D.: Application of rubber waste in road construction. Construction Review, 2009, Vol. 80, 37-44.
- Jurczak R.: Rubber (and fiber) pavement after 18 years of service. Road Engineering, 2022, №. 2-3, 35-39.
- Calabi-Floody A., Mignolet-Garrido C., Valdes-Vidal G.: Study of the effect of using asphalt binders modified with polymer fibers from end-of-life tires (ELT) on the mechanical properties of hot-mix asphalt mixtures at different operating temperatures. Materials, 2022, Vol. 15(21), 7578.
- Landi D., Marconi M., Bocci E., Germani M.: Comparative life cycle assessment of standard cellulose-reinforced and end-of-life asphalt hot mixes reinforced with tire fibers. Journal of Cleaner Production, 2020, Vol. 248, 119295.
- Landi D., Vitali S., Germani M.: Environmental analysis of different end-of-life scenarios for tire textile fibers. Procedia CIRP, 2016, Vol. 48, 508-513.